Фанера изготавливается из трех или более тонких слоев древесины, скрепленных вместе клеем. Каждый слой древесины, или фанера, обычно ориентирован так, что его волокна идут под прямым углом к соседнему слою, чтобы уменьшить усадку и повысить прочность готовой детали. Большая часть фанеры прессуется в большие плоские листы, используемые в строительстве зданий. Другие фанерные детали могут быть сформированы в простые или сложные кривые для использования в мебели, лодках и самолетах.
Использование тонких слоев древесины в качестве строительного средства датируется примерно 1500 годом до нашей эры, когда египетские мастера прикрепили тонкие куски темного черного дерева к внешней стороне кедрового гроба, найденного в гробнице фараона Тутанхамона. Эта техника позднее использовалась греками и римлянами для производства прекрасной мебели и других декоративных предметов. В 1600-х годах искусство украшения мебели тонкими кусками дерева стало известно как шпонирование, а сами куски стали называться шпоном.
До конца 1700-х годов куски шпона вырезались исключительно вручную. В 1797 году англичанин сэр Сэмюэл Бентам подал заявку на патенты, охватывающие несколько машин для производства шпона. В своих патентных заявках он описал концепцию ламинирования нескольких слоев шпона с помощью клея для формирования более толстого куска — первое описание того, что мы сейчас называем фанерой.
Несмотря на это развитие, потребовалось еще почти сто лет, прежде чем ламинированный шпон нашел какое-либо коммерческое применение за пределами мебельной промышленности. Примерно в 1890 году ламинированная древесина впервые была использована для изготовления дверей. По мере роста спроса несколько компаний начали производить листы многослойной ламинированной древесины не только для дверей, но и для использования в железнодорожных вагонах, автобусах и самолетах. Несмотря на это возросшее использование, концепция использования «склеенной древесины», как саркастически называли ее некоторые мастера, создала негативный имидж продукта. Чтобы противостоять этому имиджу, производители ламинированной древесины встретились и в конце концов остановились на термине «фанера» для описания нового материала.
В 1928 году в США были представлены первые стандартные листы фанеры размером 4 на 8 футов (1,2 на 2,4 м) для использования в качестве общего строительного материала. В последующие десятилетия усовершенствованные клеи и новые методы производства позволили использовать фанеру для самых разных целей. Сегодня фанера заменила пиломатериалы во многих строительных целях, а производство фанеры стало многомиллиардной мировой индустрией.
Внешние слои фанеры называются соответственно лицевой и тыльной стороной. Лицевая сторона — это поверхность, которая будет использоваться или видна, в то время как тыльная сторона остается неиспользованной или скрытой. Центральный слой называется сердцевиной. В фанерах с пятью или более слоями промежуточные слои называются поперечными полосами.
Фанера может быть изготовлена из твердых пород древесины, мягких пород древесины или их комбинации. Некоторые распространенные виды твердых пород древесины включают ясень, клен, красное дерево, дуб и тик. Наиболее распространенной мягкой древесиной, используемой для изготовления фанеры в Соединенных Штатах, является пихта Дугласа, хотя также используются несколько разновидностей сосны, кедра, ели и красного дерева.
Композитная фанера имеет сердцевину из древесно-стружечных плит или цельных пиломатериалов, соединенных кромкой к кромке. Она отделана лицевой и тыльной стороной из фанерного шпона. Композитная фанера используется там, где требуются очень толстые листы.
Тип клея, используемого для склеивания слоев древесины, зависит от конкретного применения готовой фанеры. Листы фанеры из хвойных пород, предназначенные для установки на внешней стороне конструкции, обычно используют в качестве клея фенолформальдегидную смолу из-за ее превосходной прочности и устойчивости к влаге. Листы фанеры из хвойных пород, предназначенные для установки на внутренней стороне конструкции, могут использовать клей на основе белка крови или соевого белка, хотя большинство внутренних листов из хвойных пород в настоящее время изготавливаются с использованием той же фенолформальдегидной смолы, что и для наружных листов. Фанера из лиственных пород, используемая для внутренних работ и в производстве мебели, обычно изготавливается с использованием мочевиноформальдегидной смолы.
В некоторых случаях требуются листы фанеры, которые имеют тонкий слой пластика, металла или пропитанной смолой бумаги или ткани, прикрепленные либо к лицевой, либо к тыльной стороне (или к обеим), чтобы придать внешней поверхности дополнительную устойчивость к влаге и истиранию или улучшить ее способность удерживать краску. Такая фанера называется фанерой с покрытием и обычно используется в строительстве, транспортной и сельскохозяйственной отраслях.
Другие листы фанеры могут быть покрыты жидкой морилкой, чтобы придать поверхности законченный вид, или обработаны различными химикатами для повышения огнестойкости фанеры или ее устойчивости к гниению.
Существует два основных класса фанеры, каждый из которых имеет свою собственную систему классификации.
Один класс известен как строительная и промышленная. Фанера этого класса используется в первую очередь из-за своей прочности и оценивается по ее способности подвергаться воздействию и сорту шпона, используемого на лицевой и оборотной стороне. Способность подвергаться воздействию может быть внутренней или внешней, в зависимости от типа клея. Сорта шпона могут быть N, A, B, C или D. Сорт N имеет очень мало дефектов поверхности, в то время как сорт D может иметь многочисленные сучки и трещины. Например, фанера, используемая для чернового пола в доме, имеет рейтинг «Внутренний CD». Это означает, что у нее лицевая сторона C и оборотная сторона D, а клей подходит для использования в защищенных местах. Внутренние слои всей строительной и промышленной фанеры изготавливаются из шпона сорта C или D, независимо от рейтинга.
Другой класс фанеры известен как лиственная и декоративная. Фанера этого класса используется в первую очередь из-за своего внешнего вида и классифицируется в порядке убывания устойчивости к влаге как техническая (внешняя), тип I (внешняя), тип II (внутренняя) и тип III (внутренняя). Их лицевые слои практически не имеют дефектов.
Размеры
Листы фанеры имеют толщину от 0,06 дюйма (1,6 мм) до 3,0 дюйма (76 мм). Наиболее распространенная толщина находится в диапазоне от 0,25 дюйма (6,4 мм) до 0,75 дюйма (19,0 мм). Хотя сердцевина, поперечные полосы, а также лицевая и обратная стороны листа фанеры могут быть изготовлены из шпона разной толщины, толщина каждого из них должна быть сбалансирована вокруг центра. Например, лицевая и обратная стороны должны быть одинаковой толщины. Аналогично, верхняя и нижняя поперечные полосы должны быть равными.
Наиболее распространенный размер листов фанеры, используемых в строительстве, составляет 4 фута (1,2 м) в ширину и 8 футов (2,4 м) в длину. Другие распространенные размеры — 3 фута (0,9 м) и 5 футов (1,5 м). Длина варьируется от 8 футов (2,4 м) до 12 футов (3,6 м) с шагом 1 фут (0,3 м). Для специальных применений, таких как строительство лодок, могут потребоваться листы большего размера.
Деревья, используемые для производства фанеры, как правило, меньше по диаметру, чем те, которые используются для производства пиломатериалов. В большинстве случаев они были посажены и выращены на территориях, принадлежащих компании, производящей фанеру. Эти территории тщательно обслуживаются, чтобы максимизировать рост деревьев и минимизировать ущерб от насекомых или пожаров.
Вот типичная последовательность операций по переработке деревьев в стандартные листы фанеры размером 4 на 8 футов (1,2 на 2,4 м):
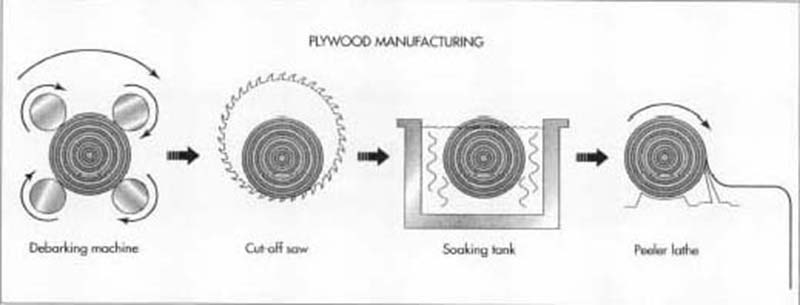
Сначала бревна окоряют, а затем распиливают на лущильные блоки. Чтобы распилить блоки на полосы шпона, их сначала замачивают, а затем распиливают на полосы.
1 Выбранные деревья на участке помечаются как готовые к рубке или вырубке. Вырубка может осуществляться с помощью бензопил или больших гидравлических ножниц, установленных спереди колесных транспортных средств, называемых валочными машинами. Ветви упавших деревьев удаляются с помощью бензопил.
2 Обрезанные стволы деревьев, или бревна, тянутся к месту погрузки колесными транспортными средствами, называемыми трелевочными тракторами. Бревна обрезаются по длине и загружаются на грузовики для поездки на фанерный завод, где они складываются в длинные штабеля, известные как бревенчатые настилы.
3 По мере необходимости бревна снимаются с палуб погрузчиками на резиновых колесах и помещаются на цепной конвейер, который доставляет их к окорочной машине. Эта машина снимает кору либо с помощью острозубых шлифовальных кругов, либо с помощью струй воды под высоким давлением, в то время как бревно медленно вращается вокруг своей длинной оси.
4 Окоренные бревна подаются на завод на цепном конвейере, где огромная дисковая пила разрезает их на секции длиной около 8 футов-4 дюйма (2,5 м) - 8 футов-6 дюймов (2,6 м), подходящие для изготовления стандартных листов длиной 8 футов (2,4 м). Эти секции бревен известны как блоки для лущения.
5 Перед тем, как можно будет резать шпон, блоки лущения необходимо нагреть и замочить, чтобы размягчить древесину. Блоки можно пропарить или погрузить в горячую воду. Этот процесс занимает от 12 до 40 часов в зависимости от типа древесины, диаметра блока и других факторов.
6 Затем нагретые блоки лущения транспортируются к токарной машине, где они автоматически выравниваются и подаются в токарный станок по одному. Поскольку токарный станок быстро вращает блок вокруг своей длинной оси, полноразмерное лезвие ножа снимает непрерывный лист шпона с поверхности вращающегося блока со скоростью 300-800 футов/мин (90-240 м/мин). Когда диаметр блока уменьшается примерно до 3-4 дюймов (230-305 мм), оставшийся кусок древесины, известный как сердцевина лущения, выталкивается из токарного станка, и на его место подается новый блок лущения.
7 Длинный лист шпона, выходящий из лущильного станка, может быть обработан немедленно или может храниться в длинных многоуровневых лотках или наматываться на рулоны. В любом случае, следующий процесс включает резку шпона на куски пригодной ширины, обычно около 4 футов-6 дюймов (1,4 м), для изготовления стандартных листов фанеры шириной 4 фута (1,2 м). В то же время оптические сканеры ищут участки с неприемлемыми дефектами, и они вырезаются, оставляя куски шпона меньше стандартной ширины.
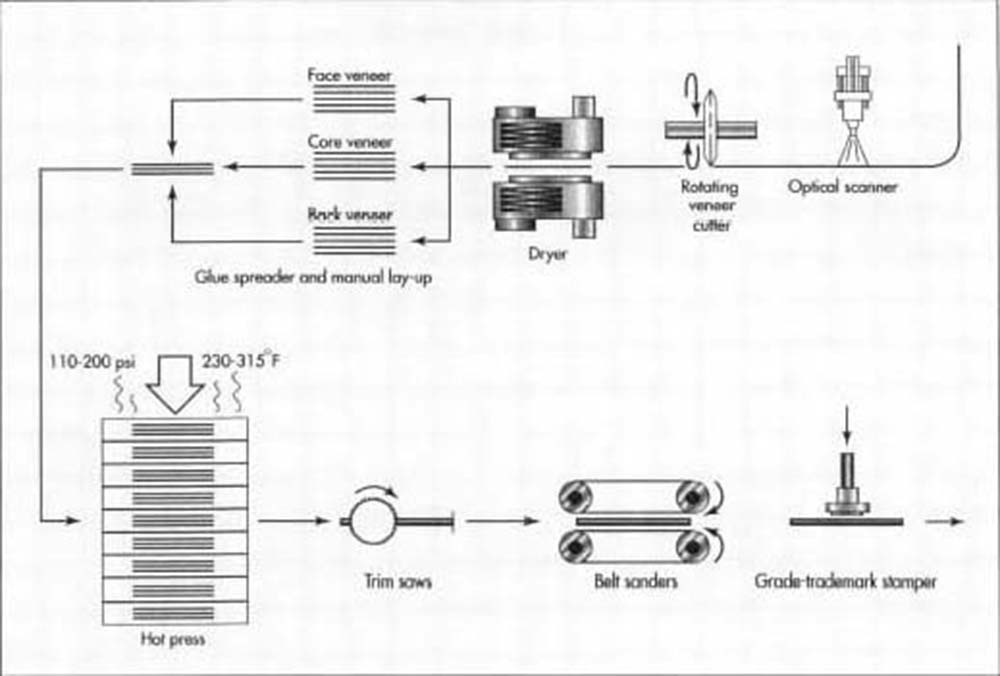
Влажные полосы шпона сматываются в рулон, а оптический сканер обнаруживает любые неприемлемые дефекты в древесине. После высыхания шпон сортируется и укладывается в стопки. Выбранные участки шпона склеиваются. Горячий пресс используется для склеивания шпона в один цельный кусок фанеры, который будет обрезан и отшлифован перед тем, как на нем будет проставлен штамп соответствующего сорта.
8 Затем секции шпона сортируются и укладываются в штабеля в соответствии с сортом. Это может быть сделано вручную или автоматически с использованием оптических сканеров.
9 Отсортированные секции подаются в сушилку, чтобы снизить их влажность и дать им усадку перед склеиванием. Большинство фанерных заводов используют механическую сушилку, в которой детали непрерывно движутся через нагретую камеру. В некоторых сушилках струи высокоскоростного нагретого воздуха продуваются по поверхности деталей, чтобы ускорить процесс сушки.
10 Когда секции шпона выходят из сушилки, они укладываются в соответствии с сортом. Секции нижней ширины имеют дополнительный шпон, сращенный с помощью ленты или клея, чтобы сделать части пригодными для использования во внутренних слоях, где внешний вид и прочность менее важны.
11 Те секции шпона, которые будут установлены поперек — сердцевина в трехслойных листах или поперечные полосы в пятислойных листах — разрезаются на куски длиной около 4 футов 3 дюйма (1,3 м).
12 Когда соответствующие секции шпона собраны для конкретной партии фанеры, начинается процесс укладки и склеивания деталей вместе. Это может быть сделано вручную или полуавтоматически с помощью машин. В простейшем случае трехслойных листов тыльный шпон укладывается плашмя и пропускается через клеенаносящий аппарат, который наносит слой клея на верхнюю поверхность. Затем короткие секции сердцевинного шпона укладываются крест-накрест поверх проклеенной тыльной стороны, и весь лист проходит через клеенаносящий аппарат второй раз. Наконец, лицевой шпон укладывается поверх проклеенной сердцевины, и лист укладывается вместе с другими листами, ожидающими отправки в пресс.
13 Склеенные листы загружаются в многопозиционный горячий пресс. Прессы могут обрабатывать 20-40 листов одновременно, при этом каждый лист загружается в отдельный слот. Когда все листы загружены, пресс сжимает их вместе под давлением около 110-200 фунтов на квадратный дюйм (7,6-13,8 бар), одновременно нагревая их до температуры около 230-315 °F (109,9-157,2 °C). Давление обеспечивает хороший контакт между слоями шпона, а тепло заставляет клей должным образом затвердеть для максимальной прочности. Через 2-7 минут пресс открывается, и листы выгружаются.
14 Затем грубые листы проходят через набор пил, которые обрезают их до окончательной ширины и длины. Листы более высокого качества проходят через набор ленточных шлифовальных станков шириной 4 фута (1,2 м), которые шлифуют как лицевую, так и обратную сторону. Листы среднего качества вручную шлифуются точечной шлифовкой для очистки грубых участков. Некоторые листы проходят через набор дисковых пил, которые вырезают неглубокие канавки на лицевой стороне, чтобы придать фанере текстурированный вид. После окончательной проверки все оставшиеся дефекты устраняются.
15 Готовые листы штампуются с маркой сорта, которая дает покупателю информацию о рейтинге экспозиции, сорте, номере завода и других факторах. Листы одного сорта-торговой марки связываются вместе в стопки и отправляются на склад в ожидании отправки.
Как и в случае с пиломатериалами, не существует идеального куска фанеры. Все куски фанеры имеют определенное количество дефектов. Количество и расположение этих дефектов определяет сорт фанеры. Стандарты для строительной и промышленной фанеры определяются Стандартом продукции PS1, разработанным Национальным бюро стандартов и Американской ассоциацией производителей фанеры. Стандарты для твердой древесины и декоративной фанеры определяются ANSIIHPMA HP, разработанным Американским национальным институтом стандартов и Ассоциацией производителей твердой древесины. Эти стандарты не только устанавливают системы классификации фанеры, но и определяют критерии конструкции, производительности и применения.
Несмотря на то, что фанера довольно эффективно использует деревья — по сути, разбирая их и собирая обратно в более прочную, более пригодную для использования конфигурацию — все еще существуют значительные отходы, присущие производственному процессу. В большинстве случаев только около 50-75% полезного объема древесины в дереве преобразуется в фанеру. Чтобы улучшить этот показатель, разрабатываются несколько новых продуктов.
Один из новых видов продукции называется ориентированно-стружечная плита, которая изготавливается путем измельчения всего бревна на стружки, а не путем снятия шпона с бревна и выбрасывания сердцевины. Стружки смешиваются с клеем и прессуются в слои с волокнами, идущими в одном направлении. Эти прессованные слои затем ориентируются под прямым углом друг к другу, как фанера, и склеиваются вместе. Ориентированно-стружечная плита такая же прочная, как фанера, и стоит немного дешевле.
Время публикации: 10-авг-2021